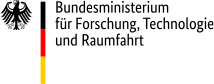
Im Projekt „MAG4INK“ wollen Wissenschaftler und Wissenschaftlerinnen des Helmholtz-Zentrums Dresden-Rossendorf (HZDR), des Fraunhofer-Instituts für Organische Elektronik, Elektronenstrahl- und Plasmatechnik (FEP) und des Fraunhofer-Instituts für Keramische Technologien und Systeme (IKTS) demonstrieren, dass sich gedruckte Magnetfeldsensoren in industrierelevanten Größenordnungen herstellen lassen.
In dem VIP+-Projekt „MAG4INK“ wird die industrietaugliche Herstellung von hochsensitiven, gedruckten Magnetfeldsensoren validiert. Was wird in dem Projekt genau gemacht und für wen ist das interessant?
Die zunehmende Digitalisierung unseres Alltags macht es immer wichtiger, große Datenmengen zu erfassen und zu verarbeiten. Ein Teil dieser Daten stammt von Sensoren die Abstände oder Geschwindigkeiten messen. Eine Vielzahl dieser Sensoren gewinnt ihre Informationen kontakt- bzw. berührungslos aus der Wechselwirkung mit Magnetfeldern. Die Kernkomponenten vieler aktuell erhältlicher Sensormodelle nach diesem Prinzip sind bisher auf starren Substraten aufgebrachte Dünnschicht-Materialien, die nicht flexibel und zudem relativ großvolumig und vergleichsweise aufwendig herzustellen sind.
Mit „MAG4INK“ wollen wir dies ändern, indem wir die elektronischen Bauteile für die Sensoren kostengünstig per Druckverfahren produzieren. Das kann man sich ähnlich wie bei einem Tintenstrahldrucker für Computerausdrucke vorstellen. In unserem Fall ersetzen wir die Druckfarben durch elektronische Funktionstinten oder -pasten. So können wir elektronische Bauelemente durch das Übereinanderdrucken mehrerer Funktionsschichten herstellen. Die so gewonnenen elektronischen Komponenten sind leicht und klein sowie dünn und flexibel – und sogar recycelbar. Im Forschungsvorhaben „MAG4INK“ wollen wir zeigen, dass sich unsere gedruckten Magnetfeldsensoren auch in einer für die Industrie interessanten Größenordnung herstellen lassen – und zwar wirtschaftlich.
Das Schlüsselelement der Pasten bzw. Funktionstinten – die magnetische Komponente – wird in einem neuartigen Verfahren produziert. Um den Gesamtprozess wirtschaftlich zu gestalten, müssen wir die jährlich herstellbare Menge des pulverförmigen Ausgangsmaterials, die sogenannten anisotropen magnetoresistiven Materialien oder kurz AMR, vom bisherigen Milligramm- in den Kilogramm-Maßstab überführen. Nur so lassen sich die Produktionskosten soweit absenken, dass der Prozess für industrielle Anwendungen interessant wird.
Die Bandbreite für Anwendungen reicht von der Raum- und Luftfahrt sowie Automobilindustrie über Technologien für das „Internet der Dinge“ bis hin zu medizinischen und textilen Anwendungen.
Wie sind Sie auf das Förderprogramm zur Validierung VIP+ aufmerksam geworden? Wieso haben Sie sich für einen Antrag in diesem Programm entschieden?
Bevor wir mit der Ausarbeitung des Projektantrags begannen, haben wir bereits gemeinsame Patentanmeldungen eingereicht und Prinzipdemonstratoren entwickelt, die das Potenzial der Technologie gezeigt haben. Auf der Grundlage dieser Vorarbeit war es möglich, realistische Validierungsziele zu definieren, von denen wir erwarteten, dass sie uns helfen könnten, die Technologie auf ein Niveau zu bringen, damit sie für weitere Technologietransferaktivitäten attraktiv wird.
In Anbetracht der Tatsache, dass der Hauptschwerpunkt unseres Projektvorschlags auf der Validierung der gesamten Produktionskette hin zur Großserienfertigung von gedruckten Magnetfeldsensoren lag, wurde das Programm „Validierung des technologischen und gesellschaftlichen Innovationspotenzials wissenschaftlicher Forschung – VIP+“ des BMBF vom Konsortium priorisiert, da es alle relevanten Schritte der Validierung unterstützt.
Welche Arbeiten haben Sie im Rahmen des Projekts bislang durchgeführt? Wie hat Sie das Programm VIP+ unterstützt?
Auf technischer Seite befinden wir uns in der Endphase des Projektverlaufes. Wir haben alle kritischen Aspekte der Herstellungskette validiert und gezeigt, dass die Herstellung von einigen Kilogramm hochwertiger magnetoresistiver Paste pro Jahr möglich ist. Mit dieser Menge können größenordnungsmäßig mehr als 1.000.000 Sensoren gefertigt werden. Darüber hinaus haben wir eine kosteneffiziente Nachbehandlung gedruckter Magnetfeldsensoren mithilfe einer großflächigen Laserbestrahlung etabliert, die eine gute elektrische und magnetoresistive Leistung für MAG4INK-Sensoren ermöglicht. Wir haben unsere gedruckten Sensoren bereits erfolgreich in Funktionsmuster berührungsloser Schalter für Mensch-Maschine-Schnittstellen sowie Sicherheitsanwendungen integriert.
Zudem konnten wir – auch durch die Unterstützung unserer Innovationsmentoren - Feedback von anwendungsorientierten Forschungseinrichtungen und der Industrie einholen, um unsere Validierungsaktivitäten auf die Bedürfnisse der Anwender hin zu optimieren.
Da der Hauptschwerpunkt unseres Projektvorschlags auf der Validierung der Produktionskette hin zur Großserienfertigung von gedruckten Magnetfeldsensoren lag, war VIP+ für uns das relevante Programm für unser Vorhaben. Mit der Förderung konnten unsere Expert:innen ausreichend Tests zur Optimierung der Prozesskette durchführen und wir konnten die technisch notwendige Ausrüstung für die Skalierungsarbeiten finanzieren.
Wir hatten die Gelegenheit, unsere MAG4INK-Projektskizze während einer Infoveranstaltung zum Programm VIP+ vorzustellen und zu diskutieren. Das positive Feedback, das wir bekamen, hat uns motiviert, den MAG4INK Projektantrag auszuarbeiten. Auch andere Kollegen und Kolleginnen lobten das Programm, was eine besondere Flexibilität der Förderung bietet: Jederzeit und in allen Themenbereichen einreichen zu können.
Unsere Demonstratoren werden wir auf international bedeutenden Messen im Bereich der gedruckten Elektronik, wie der LOPEC 2023 in München sowie auf einer ganzen Reihe Veranstaltungen für die bereitere Öffentlichkeit - wie der Langen Nacht der Wissenschaften in Dresden - präsentiert. Da die in MAG4INK entwickelte Technologie neu ist, gibt es natürlich noch keine Lehrbücher oder Universitätskurse zu diesem Thema. Daher sind das auch spannende Ergebnisse für junge Wissenschaftler und Wissenschaftlerinnen.
Läuft das Validierungsvorhaben wie geplant? Sind Sie mit Ihren bisherigen Ergebnissen zufrieden?
Wir haben unser Projekt im April 2021 während der COVID-Pandemie gestartet. Daher waren erste Schritte bei der Umsetzung des Projekts von den damit verbundenen Einschränkungen betroffen. Dank des großen Engagements der Konsortialpartner gelang es uns in dieser Anfangsphase trotzdem, das Team mit jungen Forschern und Forscherinnen zu vervollständigen, eine effiziente Probenherstellung sowie einen effizienten Austausch mit dem Projektbeirat zu etablieren. Rückblickend auf die letzten rund 2,5 Jahre Projektlaufzeit können wir bestätigen, dass das Förderprojekt nach Plan läuft und alle vorgesehenen Meilensteine erfolgreich und rechtzeitig erreicht wurden. Das Projekt hat in der Forschungsgemeinschaft und in der Industrie bereits große Aufmerksamkeit gefunden. Wir haben neue Ideen für Folgeprojekte zur grundlegenden Materialwissenschaft und zum Technologietransfer entwickelt. Wir werden regelmäßig von interessierten Branchenvertretern bezüglich des aktuellen Stands der MAG4INK-Technologie angesprochen, was auch ein Zeichen dafür ist, dass das Projekt auf einem guten Weg ist. Wir schätzen den großen Einsatz der Beiratsmitglieder und ihren immer wieder anregenden Input bei der Umsetzung des Projekts sehr. Diese Anregungen helfen uns nicht nur bei der Entwicklung der MAG4INK-Technologie, sondern auch dabei, die realisierten Demonstratoren entsprechend der neuen Anwendungsszenarien zu optimieren.
Welche Möglichkeiten sehen Sie für die Verwertung der Ergebnisse? Welche Anwendungen oder Produkte könnten durch Ihre Sensoren nachhaltig verändert oder gar revolutioniert werden?
MAG4INK ermöglicht einen völlig neuen Ansatz in der Magnetoelektronik. Im Gegensatz zu herkömmlichen Magnetfeldsensoren auf starren Substraten, die komplexe und teure Lithographietechnologien erfordern, konnten wir zeigen, dass sich leistungsstarke Magnetfeldsensoren mithilfe kosteneffizienter Druckverfahren im großen Maßstab herstellen lassen. Dies erschließt der Magnetoelektronik neue Anwendungen, die vorher nicht oder nur sehr eingeschränkt möglich waren. Die mechanische Flexibilität der Sensoren gewährleistet ihre Integration in Wearables oder komplex geformte Objekte. Beispielsweise können Magnetfeldsensoren auf jede Oberfläche, einschließlich Tapeten oder extrem dünnen, flexiblen Kunststofffolien, gedruckt oder im Sinne von Smart-Home-Anwendungen in großflächige Interaktionsflächen umgewandelt werden. Darüber hinaus können leichte, flexible und sogar gedruckte Magnetfeldsensoren in Textilien (z. B. Smart Wearables) integriert werden, um die Überwachung der Bewegung von Körperteilen für Fitness-, Lifestyle- oder Rehabilitationszwecke zu ermöglichen. Damit steht jetzt eine Technologie für eine effiziente Produktion von Millionen Sensoren zur Verfügung. Zusammen mit der Massenproduktion könnte das die gesamte Anwendungsstrategie für Magnetfeldsensoren revolutionieren.
Wir sind sehr stolz, dass es uns im Rahmen der Projektumsetzung zudem gelungen ist, ein völlig neues Konzept für gedruckte nachhaltige Magnetfeldsensoren zu entwickeln. In diesem Zusammenhang haben wir in einer international führenden Zeitschrift einen Artikel zur Realisierung selbstheilender Magnetfeldsensoren veröffentlicht [Nature Communications 13, 6587 (2022)]. Derzeit werden Magnetfeldsensoren am Ende ihrer Lebensdauer einfach entsorgt und landen im Elektronikschrott. Angesichts der Tatsache, dass Magnetfeldsensoren umweltschädliche Materialien enthalten, ist es wichtig, Methoden zur Reparatur defekter Sensoren zu entwickeln, um ihre Lebensdauer zu verlängern. Dies ist besonders bedeutsam für Smart Wearables, bei denen Schäden am Sensor durch das Tragen und Waschen kaum zu vermeiden sind. Die Möglichkeit Magnetfeldsensoren zu reparieren ist daher ein erster Schritt in Richtung Nachhaltigkeit der Magnetoelektronik.
Wir sind sogar noch weitergegangen: in ersten Versuchen haben wir gezeigt, dass Magnetfeldsensoren auch auf der Basis vollständig biokompatibler und biologisch abbaubarer Materialien gedruckt werden können. Dieser Demonstrator ist weltweit der erste und zeigt, dass eine vollständig ökologisch nachhaltige Magnetoelektronik realisiert werden kann. Das Konzept wurde im Rahmen des MAG4INK-Projekts entwickelt und wird vom Projektkonsortium genutzt, um weitere Aktivitäten zu nachhaltigen Magnetfeldsensoren weltweit zu initiieren. Die Realisierung biologisch abbaubarer und biokompatibler Magnetfeldsensoren wird wesentlich zur Minimierung des Elektroschrotts beitragen und die Menge an giftigen und kritischen Materialien begrenzen, die für die Herstellung von Magnetfeldsensoren verwendet werden. Diese Aktivitäten stehen im Einklang mit den Zielvorgaben der Bundesregierung sowie der Europäischen Union.
Zuwendungsempfänger (Koordinator)
Helmholtz-Zentrum Dresden-Rossendorf e.V.
Bautzner Landstr. 400, 01328 Dresden
Projektleiter
Herr Dr. Denys Makarov
Tel.: +49 (0) 351 260-3273
E-Mail: d.makarov@hzdr.de
Weiter Informationen zum Projekt MAG4INK