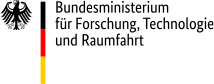
Medizinprodukte wie Implantate stehen in direktem Kontakt mit dem menschlichen Körper – deshalb werden sie vor dem Eintritt in den Markt und ihrem Einsatz besonders umfangreich getestet. Ein großer Teil dieser Tests findet im Labor mithilfe von Zellproben statt.
Auch weil die zu prüfenden Dinge, die sogenannten Prüfkörper, beispielsweise ganz unterschiedliche Formen und Oberflächen haben, stellen quantitative Vergleichstests im direkten Kontakt zwischen Zelle und Material eine Herausforderung dar. Ein universell einsatzbares Testsystem, welches quantitative Vergleichstests ermöglicht, steht im Projekt UniBioFace im Fokus. Darüber haben wir mit Projektkoordinatorin Dr. Susanne Kurz gesprochen.
Frage: Wie gleicht Ihr Testsystem die bestehenden Unterschiede in den zu testenden Medizinprodukten aus?
Dr. Susanne Kurz: Wir haben ein modulares In-vitro-Testsystem entwickelt, das es ermöglicht, unterschiedlichste Prüfkörper – egal ob glatt, rau, flexibel oder fest – in einem einheitlichen Setup zu testen. Dabei sorgt ein cleveres mechanisches Design für einen fluiddichten Verschluss, und zwar ganz ohne den Einsatz von Kleber. So können wir erstmals sicherstellen, dass biologische Tests wirklich vergleichbar sind, unabhängig vom Material oder von der Oberfläche. Wir bauen im Projekt auf ein erprobtes System für Zellkulturen auf. Dabei geht es um standardisierte, kleinformatige Kultivierungsgefäße, die in der Zellkultur bereits verwendet werden. Sie haben 96 kleine Vertiefungen (englisch: wells), in denen Zellen kultiviert werden können, um Tests durchzuführen. Auch unser System arbeitet mit den klassischen 96er wells auf den Oberflächen. Diese Anzahl und Systemstruktur ist also nicht zufällig gewählt, sondern in der Praxis bereits etabliert.
Was sind die genauen Vorteile Ihrer Entwicklung?
Das Besondere ist: Unser System erlaubt standardisierte, quantitative Tests – und das auf Prüfkörpern mit völlig unterschiedlichen Oberflächen. Damit lösen wir ein zentrales Problem der bisherigen Materialtests. Gleichzeitig sparen wir Ressourcen, weil wir mehrere Datenpunkte pro Probe erheben können. Für Forschende ebenso wie für Prüflabore bedeutet das: bessere Datenqualität, effizientere Abläufe und ein echter Gewinn bei Zeit, Kosten und Aussagekraft.
Ihre Entwicklung hat verschiedene Stadien durchlaufen und sich dabei stark gewandelt. Wie sind Sie bei der jetzigen Lösung gelandet?
Ganz ehrlich: Am Anfang hatten wir eine Idee – aber keine fertige Lösung. Erst durch viele Rückmeldungen aus der Praxis, zahllose Tests mit unterschiedlichsten Materialien und ein bisschen Trial and Error, also viele Versuche, haben wir die heutige Systemarchitektur gefunden. Der Schlüssel war die enge Zusammenarbeit mit potenziellen Anwendenden. Dadurch konnten wir gezielt Anforderungen ableiten und unser Design kontinuierlich verbessern.
Welche Rolle hat die Validierungsförderung im Prozess gespielt?
Die Förderung im Programm VIP+ war für uns essenziell. Ohne diese Unterstützung hätten wir die Validierung nie in dieser Tiefe und mit diesem Anspruch stemmen können. Sie hat uns ermöglicht, das System auf Herz und Nieren zu testen und so in Richtung Marktreife zu bringen. Außerdem konnten wir unser Netzwerk ausbauen – von Forschenden über Prüflabore und Industriepartner bis hin zur weiteren Vertiefung unserer langjährigen Mitarbeit in den ISO-Gremien zur biologischen Evaluierung von Medizinprodukten. Die Förderung hat uns zudem die Möglichkeit gegeben, umfassend zu prüfen und zu planen, wie eine Patent-Verwertung und die Einführung des Systems in den Markt gelingen können.
Wie sind jetzt die nächsten Schritte für Ihre Entwicklung?
Um den Transfer des Systems in die Praxis erfolgreich zu meistern und somit die Vorteile für die wissenschaftliche Datenerhebung einer breiten Öffentlichkeit zugänglich zu machen, steht nun der finale Schritt an – die konkrete Verwertung. Genau daran arbeiten wir jetzt mit Hochdruck und sprechen mit potenziellen Lizenznehmern. Unser Ziel ist, bis Ende 2026 das System in wissenschaftlichen Laboren und Prüflaboren routinemäßig im Einsatz zu haben – als neuer Standard für entwicklungsbegleitende und präklinische Materialtests.
Kontakt
Dr. Susanne Kurz
Fraunhofer-Institut für Keramische Technologien und Systeme IKTS, Leipzig
+49 341 35536-3412
susanne.kurz@ikts.fraunhofer.de
Weitere Informationen zum Projekt UniBioFace:
https://www.validierungsfoerderung.de/validierungsprojekte/unibioface